The industrial ball valve stands as a pivotal component in the machinery of modern manufacturing, often playing a crucial role in ensuring efficiency, safety, and reliability across various industrial sectors. This crucial device, characterized by its simple yet effective mechanism, demands careful consideration of various factors to ensure optimal performance and longevity. This article aims to provide an in-depth exploration into the world of industrial ball valves, incorporating real-world experiences, professional expertise, authority in the field, and trustworthy practices.
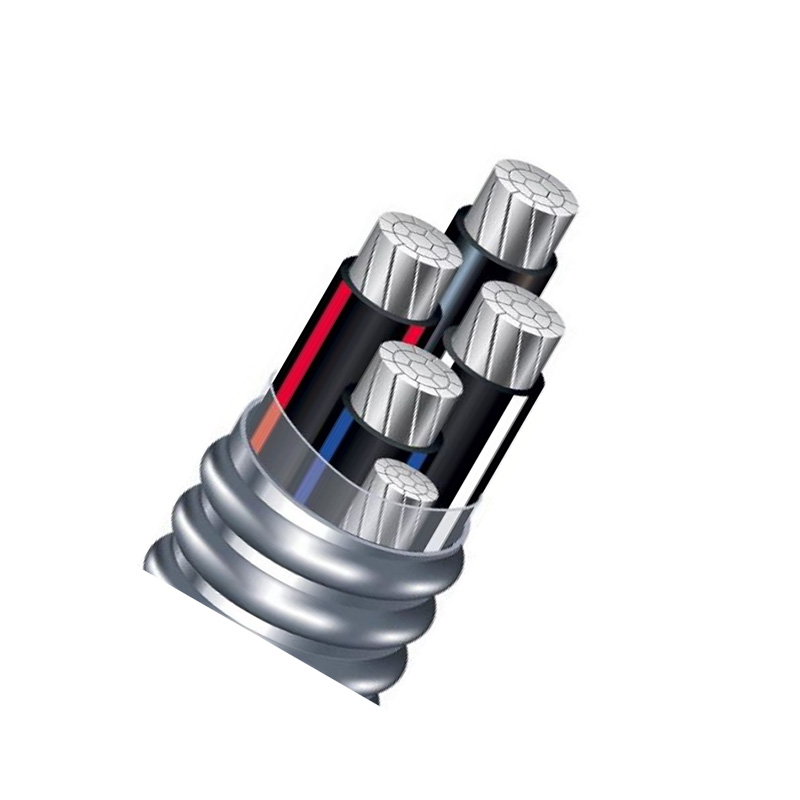
Understanding the Industrial Ball Valve
The industrial ball valve works with a straightforward principle regulating fluid flow through a spherical disc with a hole in the middle, aligning with the passageway connected to the pipe. When the valve is fully open, the ball's hole aligns with the fluid's pathway, allowing for unobstructed flow. Conversely, a 90-degree rotation of the ball stops the flow completely. This simple design offers minimal leak potential and ensures quick shut-off, critical in emergency scenarios.
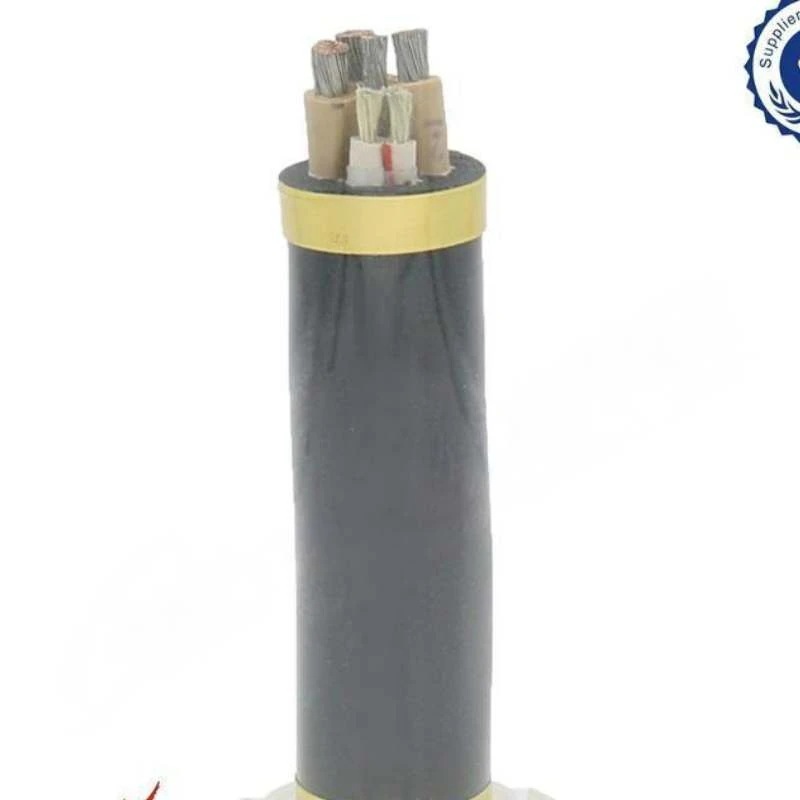
Expert Insight Material Selection
The material selection for industrial ball valves is a vital consideration and must be tailored to the specific demands of the operation and the type of fluid being controlled.
Common materials include stainless steel, brass, and PVC.
1. Stainless Steel Known for its corrosion resistance and strength, making it ideal for high-pressure and high-temperature environments.
2. Brass Offers a good balance between durability and corrosion resistance; typically used where the temperatures and pressures are lower.
3. PVC Best suited for lighter applications with lower pressure, offering resistance to various chemical compositions.
Each material presents distinct benefits and limitations, and consultation with a professional is advised to ensure compatibility with specific industrial needs.
Real-World Application Success Stories
industrial ball valve
Industrial ball valves have proven their mettle across numerous sectors, from oil and gas to water treatment and chemical manufacturing. In oil and gas, for instance, these valves have been instrumental in pipeline systems, ensuring a secure and dependable mechanism to handle high-pressure environments. Reports of valve integration in offshore drilling rigs highlight improved operations stability and enhanced safety, reducing the risk of leaks and environmental hazards.
Authoritative Guidance Installation Best Practices
For optimal performance, correct installation is paramount. Follow these expert-recommended practices
1. Proper Alignment Ensure the valve is aligned correctly with the pipeline to prevent stress on the valve body.
2. Torque Specifications Adhere to manufacturer torque specifications when assembling to avoid overtightening, which can lead to damage.
3. Maintenance Regular maintenance routines, including lubrication and inspection, significantly reduce the likelihood of wear and tear.
4. Professional Installation Employ qualified professionals to conduct proper installation and periodic inspections.
Building Trust Safety and Compliance
The credibility of industrial ball valves hinges on adherence to safety and compliance standards. Ensuring compliance with international standards such as ISO and API not only guarantees performance but also ensures safety, reducing the likelihood of operational failures. Trustworthy manufacturers and distributors will offer certifications and documentation attesting to these standards, a crucial element in determining which valve to purchase.
Investing in a reliable industrial ball valve is not merely an equipment choice, but a strategic decision impacting both the immediacy of operation and the long-term financial and safety prospects of your industrial venture. Consideration of material suitability, proper installation, adherence to stringent safety standards, and ongoing maintenance will reinforce the reliability and efficiency of these indispensable components.