When it comes to industrial flow control, cast steel valves stand out for their durability and reliability. Offering robust construction and versatility, these valves are pivotal in handling high-pressure applications across various industries. Their reputation for strength and longevity sets cast steel valves apart as an essential component in complex systems, particularly where dependable performance is a mandate.

Cast steel valves are manufactured through a precise casting process that allows for the creation of intricate shapes and the inclusion of complex features without compromising their structural integrity. This process ensures that the resulting valves can withstand high-pressure environments and corrosive substances. Unlike other materials that may falter under extreme temperatures or corrosive conditions, cast steel offers superior resistance, making it the ideal choice for industries like oil and gas, power generation, and chemical processing.
The expertise involved in the production of cast steel valves is significant. Professionals in this field must understand the nuances of metallurgy, potential stress points, and the dynamics of flow control to deliver products that meet stringent quality standards. The choice of materials, alongside adherence to production protocols, guarantees that these valves offer a long service life, even under the harshest conditions.
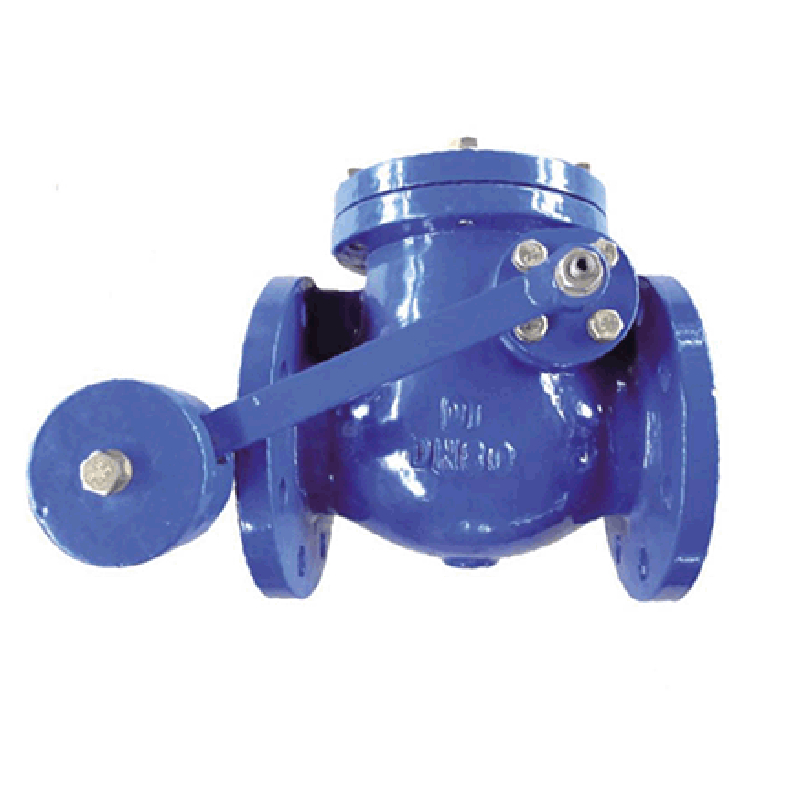
Key to the cast steel valve’s authority in the market is its performance in critical applications.
Industries that cannot afford downtime rely on these valves for their reliable sealing and high tolerance to pressure variations. Tests and certifications, such as ISO or API standards, further cement their credibility, ensuring that these valves meet international safety and performance benchmarks. When it comes to system efficiency and safety, cast steel valves are often the first choice for engineers and procurement specialists.
cast steel valve
The trust in cast steel valves is built on years of proven performance and stringent testing. Manufacturers often provide detailed data sheets, performance graphs, and test results that offer transparency into the valve’s capabilities. This transparency, combined with a history of successful deployment in various sectors, builds a strong foundation of trust with consumers. In addition, many manufacturers offer warranties and ongoing support, reassuring customers of their investment's longevity and reliability.
In practical terms, selecting the right cast steel valve entails understanding specific application needs such as the type of medium, temperature, and pressure requirements. Technical experts typically stress the importance of consulting with professionals or working with experienced suppliers to ensure a suitable match between valve specifications and intended use. This collaboration not only maximizes the valve's effectiveness but also enhances the safety and efficiency of the entire system.
Moreover, advancements in technology have enabled further improvements in cast steel valves, including enhancements in design and functionality. Today’s models might feature innovations like reduced friction components or self-cleaning capabilities, ensuring minimal maintenance needs and extended service intervals. By adopting the latest technologies, manufacturers continue to improve the reliability and efficiency of their valves, aligning with modern energy and sustainability goals.
In conclusion, cast steel valves remain a cornerstone of industrial applications due to their strength, reliability, and ability to perform under demanding conditions. Their development is a testament to the cumulative expertise and credibility amassed over decades. As industries evolve, the continued enhancement and adaptation of cast steel valves demonstrate their indispensable role in achieving operational excellence and safety in industrial processes.