In the intricate world of fluid dynamics and piping systems, the check valve emerges as an unsung hero, championing efficiency and safety in numerous applications. These devices are critical components in various industries, protecting equipment, ensuring correct operations, and preventing potentially disastrous reverse flows.
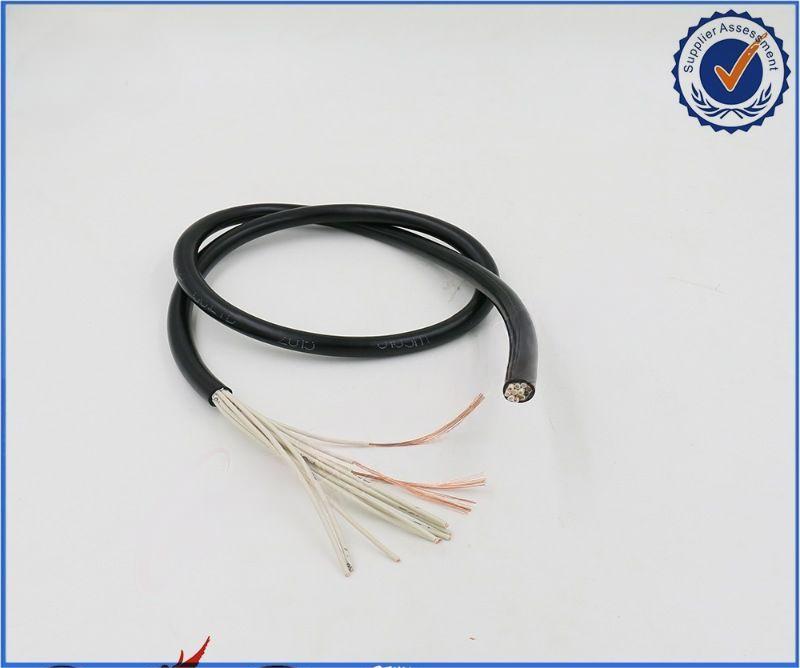
At the core, check valves are designed to allow fluid to flow in one direction while preventing it from flowing in the wrong direction. This seemingly simple functionality plays a vital role in protecting pumps and compressors from damage due to backflow, maintaining pressure within systems, and supporting overall system integrity.
When evaluating check valves, understanding different types and their specific applications is paramount for maximizing system performance and reliability. Common types include swing check valves, lift check valves, and ball check valves, each with unique characteristics suited to specific conditions. For instance, swing check valves are advantageous in systems with high flow rates, given their low-pressure drop and robust design. Conversely, lift check valves are preferred in high-pressure environments due to their straightforward operational mechanism.
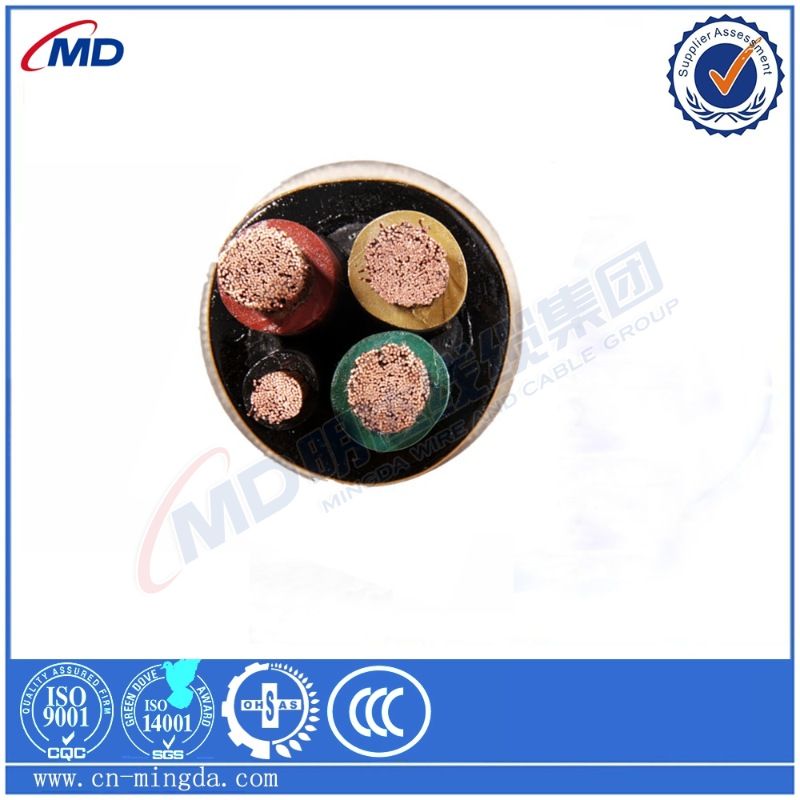
In the realm of expertise, selecting the appropriate check valve involves assessing system parameters like pressure, temperature, and flow rate, alongside fluid characteristics such as corrosiveness or abrasiveness. Advanced materials, from stainless steel to specialized polymers, should be carefully considered to match the media and environmental conditions, ensuring longevity and performance.
Trusted information from industry experts indicates that proper installation and maintenance of check valves is critical. Installation should ensure correct alignment and avoid unnecessary strain,
while regular maintenance checks focus on signs of wear or blockage to prevent valve failure. These practices safeguard system efficacy and extend the operational life of the check valve, aligning with best practices in fluid system management.
check valve
Furthermore, technological advancements have propelled check valve capabilities far beyond traditional models. Modern check valves incorporate smart technologies for remote monitoring and diagnostics, elevating their role in predictive maintenance strategies. This evolution underscores the importance of staying abreast of technological trends within the industry to ensure systems are both current and resilient against emerging challenges.
From an authoritative perspective, industry standards and certifications are key indicators of quality and reliability in check valves. These standards, provided by organizations such as the American National Standards Institute (ANSI) or the International Organization for Standardization (ISO), ensure products meet rigorous performance criteria, providing reassurance to industry professionals and stakeholders.
Building trust in your choice of check valve involves not only relying on certified standards but also engaging with reputable manufacturers known for their commitment to quality and innovation. Companies that invest in research and development, offer comprehensive support services, and have a proven track record of performance contribute significantly to system reliability and efficiency.
In conclusion, the selection and management of check valves is a sophisticated process that benefits greatly from experience, expertise, authority, and trust. By leveraging these elements, professionals can ensure their fluid systems are safe, efficient, and sustainable, thereby optimizing operational outcomes across diverse industrial landscapes.