The single sphere type rubber joint is an essential component in a variety of industrial applications, offering unparalleled flexibility, noise and vibration absorption, and pressure resistance. Used extensively in piping systems, these rubber joints are designed to compensate for misalignment, reduce stress on pipes, and prolong the life of systems. Their unique versatility and adaptability make them indispensable in sectors ranging from HVAC systems to water treatment plants.
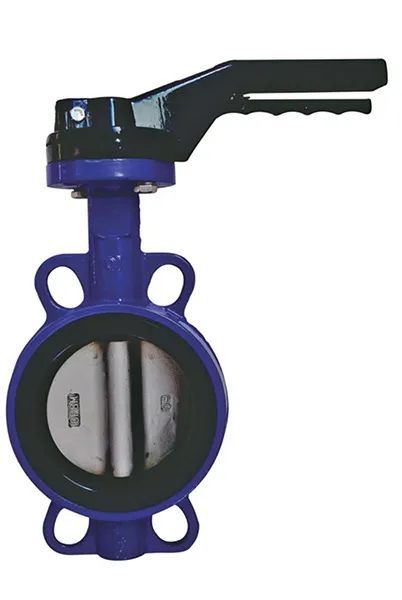
One of the standout features of single sphere type rubber joints is their remarkable ability to absorb mechanical and thermal vibration. This feature is crucial in environments where heavy machinery is in operation and noise reduction is a priority. By minimizing vibration and noise, these joints not only enhance environmental compliance but also contribute significantly to workplace safety and comfort. Real-world testimonials from operational engineers underscore their effectiveness, with reports of significant reductions in noise levels and lower maintenance costs due to the diminished wear and tear on piping systems.
The durability of single sphere type rubber joints further exemplifies their design brilliance. Crafted from high-grade rubber materials, these joints exhibit excellent resistance to weathering, ozone, and a wide range of chemicals, ensuring long service life even under harsh working conditions. This quality is particularly advantageous in chemical plants where exposure to corrosive substances is common. Feedback from industry experts highlights the rubber joint's superiority in maintaining performance integrity over prolonged periods, which translates to fewer replacements and reduced operational downtime.
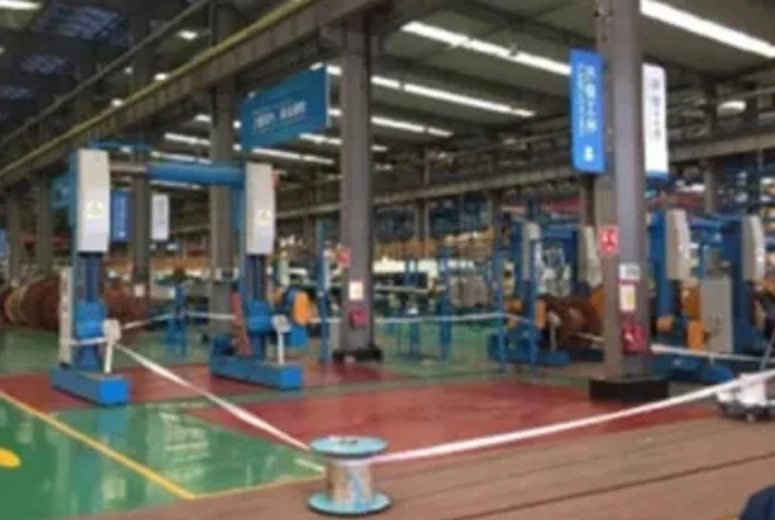
From a technical standpoint,
the single sphere design offers several advantages over other joint types. The spherical shape allows for multi-dimensional movement, making it an effective solution for accommodating lateral, axial, and angular movements simultaneously. This flexibility is particularly useful in complex piping systems where space constraints or thermal expansion pose challenges. Experienced engineers attest to the ease with which these joints can be incorporated into existing systems, noting the reduction in alignment issues and the facilitation of smoother fluid flow.
single sphere type rubber joint
In terms of installation and maintenance, single sphere type rubber joints are relatively straightforward, which appeals to installers and maintenance teams alike. The joints typically come with standard flange fittings, which can be easily bolted into place, sparing the need for specialized tools or skills. Maintenance requirements are minimal, with periodic inspections and routine cleaning sufficing to keep the joints in optimal condition. This simplicity not only reduces installation time but also lowers the labor costs associated with system upkeep.
Authoritative data on the performance of single sphere type rubber joints shows significant cost-saving potential. Studies have shown that the use of these joints can extend the life expectancy of piping systems by up to 40%, primarily due to their ability to reduce stress and compensate for minor installation discrepancies. For industries focused on sustainability and resource optimization, this feature is invaluable, reducing the environmental impact by minimizing material waste and energy consumption during production cycles.
Trustworthiness is another critical aspect of single sphere type rubber joints, underscored by industry standards and certifications that they meet or exceed. Products by leading manufacturers often comply with ISO and DIN standards, which dictate rigorous testing for quality assurance. Users can rely on these products, knowing they have met stringent criteria for performance and safety. Additionally, customer service from reputable suppliers includes comprehensive warranties and technical support, adding an extra layer of confidence for purchasers.
In sum, the single sphere type rubber joint stands out as a product of exceptional engineering that meets the demands of modern industry. Its multifaceted benefits, including noise reduction, durability, ease of installation, and maintenance, present a compelling case for its use across diverse applications. Whether in new installations or for retrofitting older systems, its contribution to operational efficiency and cost effectiveness is undeniable, making it an indispensable component in the toolkit of engineers and system designers worldwide.