In the industrial world, equipment quality can make or break a project, and one component that stands out for its steadfast reliability is the 6-inch ball valve. This versatile tool, weighing heavily in both importance and construction, serves as a cornerstone in various sectors such as oil and gas, manufacturing, and water treatment facilities. To truly appreciate the significance of this device, one must delve into its unique attributes and practical applications.
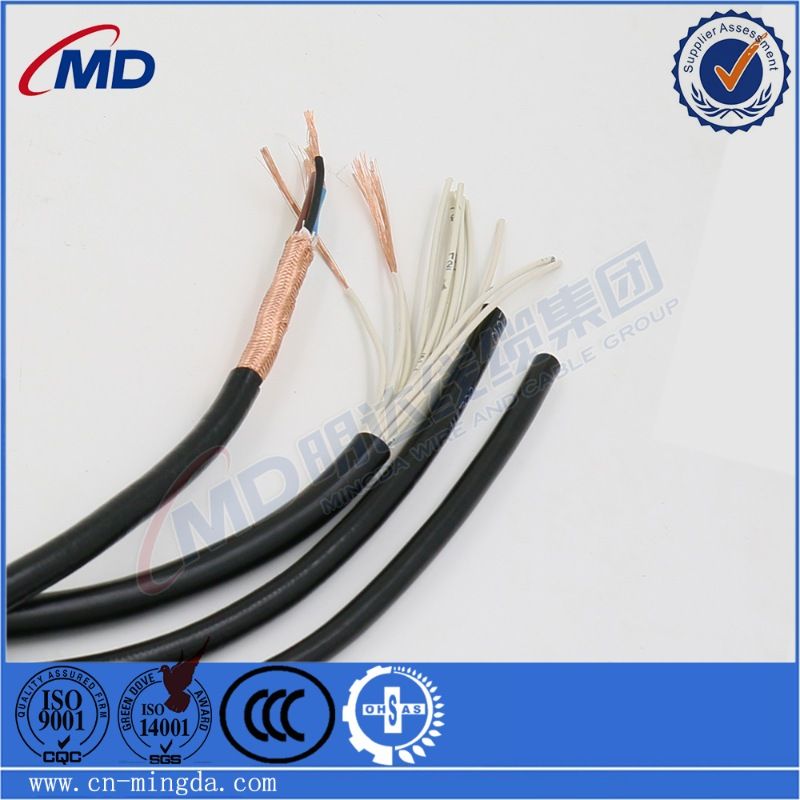
The 6-inch ball valve is admired for its precision and durability. Manufactured often from robust materials such as stainless steel, brass, or cast iron, these valves need to be both resilient and capable of withstanding intense conditions, including high pressure and extreme temperatures. The construction of a ball valve includes a spherical disc — aptly referred to as a “ball” — that controls the flow through it. The ball features a central hole, or port. When the valve is in the operational on position, the hole aligns with the flow path, allowing fluid to pass through. Conversely, when rotated, it effectively seals the passage, offering an immediate stop to flow. This ability to provide instant shutoff drastically reduces the risk of leaks and potential damage to the infrastructure.
Within industries requiring stringent safety protocols, such as chemical processing or petroleum refining, the reliability of a ball valve cannot be overstated. These valves need to demonstrate exceptional airtight sealing, known as zero leakage, to safeguard not only the equipment but also the personnel working around potentially hazardous materials. One of the contributing factors to this reliability is the valve's full bore design, which ensures that the flow path is unobstructed, reducing turbulence and wear. This feature extends the lifespan of the system and mitigates pressure drop, which is critical for maintaining efficiency in large-scale operations.
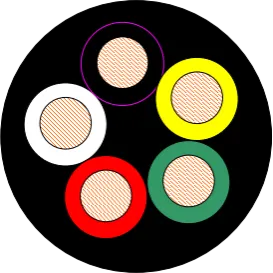
The expertise required to manufacture and maintain a 6-inch ball valve cannot be ignored. Precision engineering is at the heart of each valve's production process. It requires skilled technicians who carry out meticulous inspections and employ advanced computer-aided design (CAD) systems to ensure that every valve meets and often exceeds industry standards such as those set by the American Petroleum Institute (API) and International Organization for Standardization (ISO). These certifications not only vouch for the product's quality but also assure users of its performance in real-world conditions.
6 inch ball valve
When selecting a ball valve, it is crucial to evaluate factors including pressure ratings, material compatibility, and specific application requirements. Each of these elements contributes to the valve's overall authority in its application since inappropriate selection can lead to system inefficiencies or even catastrophic failures. Reliable manufacturers provide comprehensive guidance and data sheets for these selections, which speaks to the trustworthiness of both the product and the supplier.
Equipped with expert knowledge and a commitment to quality, industry professionals can derive immense benefits from leveraging these valves within their systems. Regular maintenance, as well as performance checks, ensure that the 6-inch ball valve operates at optimal capacity throughout its lifecycle. This proactive approach not only validates the valve's trustworthiness but also optimizes the return on investment by minimizing downtime and repair costs.
In summary, the 6-inch ball valve is not just a component but a critical investment in industrial resilience and efficiency. Its expertly crafted design, combined with robust construction, positions it as an authoritative solution in managing flows under rigorous conditions. With its proven track record for reliability, these valves continue to earn the trust of industry leaders worldwide, fortifying their applications with precision, safety, and enduring performance.