Butterfly valves, an essential component in fluid control systems, are gaining increasing popularity due to their efficient and cost-effective design. In the realm of butterfly valves, it is crucial to distinguish between the wafer butterfly valve and the lugged butterfly valve as each has unique features and applications.
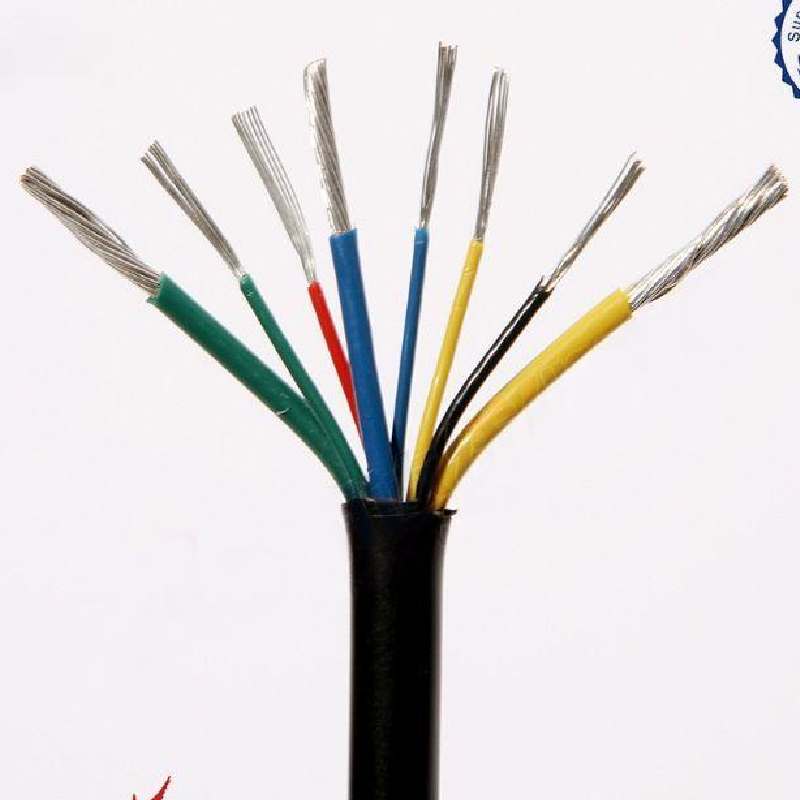
Having worked with industrial fluid systems for over a decade, my experience with wafer and lugged butterfly valves has revealed their distinct advantages and nuances. Wafer butterfly valves are designed to maintain a seal against bi-directional pressure, preventing backflow in systems. Their compact structure is ideally suited for applications where space is a constraint, allowing for easy installation between flanges of larger pipeline setups. This design reduces install and maintenance costs while maintaining high performance.
Professionals looking for a valve option that offers quick operation and low-pressure drop will find wafer butterfly valves appealing. Their streamlined design ensures minimal fluid resistance, which can lead to significant energy savings, especially valuable in large operations.
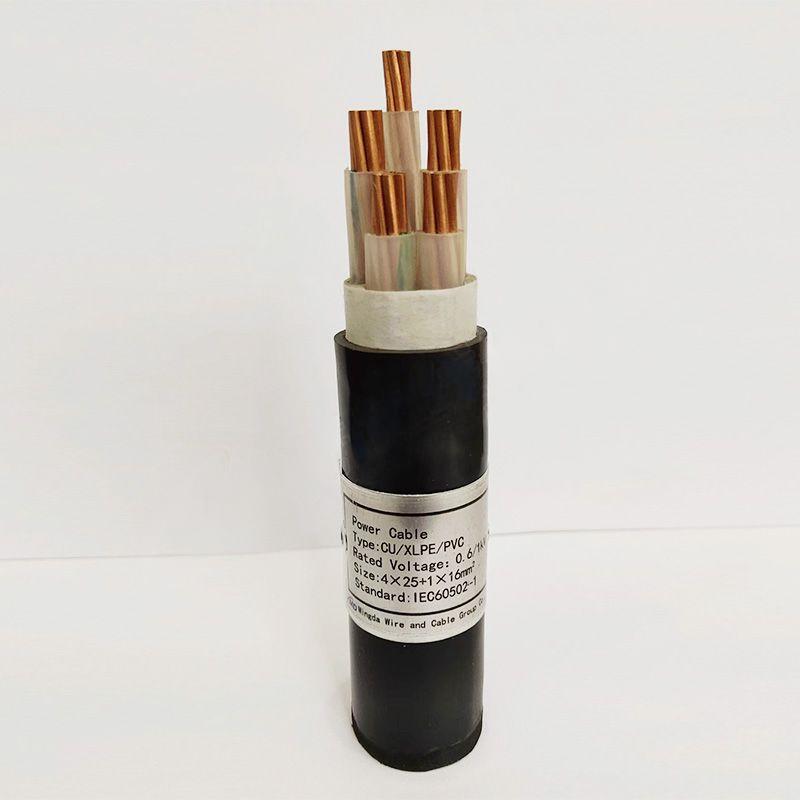
Lugged butterfly valves, on the other hand, provide a higher level of flexibility and ruggedness. Their standout feature is the threaded inserts, or “lugs,” surrounding the valve body, enabling valves to be placed in dead-end service without the need for downstream piping. This capability not only simplifies maintenance tasks but can also lead to extended service life of pipelines by allowing for isolated system shutdown.
From an expertise standpoint,
lugged butterfly valves are highly favored in scenarios where pipeline integrity is paramount. Industries dealing with hazardous or high-pressure materials benefit significantly as the lugged design withstands higher stress levels, ensuring reliable and continued flow control.
wafer and lugged butterfly valve
The choice between a wafer and lugged butterfly valve can impact operational efficiency, safety, and cost. Authoritative guidance suggests that industries such as chemical manufacturing, water treatment, and food processing should lean towards lugged butterfly valves for enhanced safety and durability.
While wafer butterfly valves might be preferable in systems where space optimization and economic considerations are primary concerns, one must not overlook the application's specific requirements and environmental conditions. A valve's compatibility with particular fluids, pressure ratings, and closure needs should always be reviewed in detail.
In terms of trustworthiness, partnering with verified manufacturers and suppliers ensures that the valves meet industrial standards, such as API 609 or ISO 5752, fostering confidence in their performance. Engaging with reputable brands not only guards against counterfeits but also typically provides additional benefits like comprehensive after-sales support, installation guidance, and warranties.
In conclusion, understanding the nuances and technical specifications of wafer and lugged butterfly valves elevates one's ability to choose the right valve for specific applications. Knowledgeable selection based on a thorough evaluation of operational needs and environmental considerations ensures optimal performance and longevity. As the fluid control industry evolves, staying informed on advancements and best practices will continue to be pivotal for operational success and safety.