High performance butterfly valves are integral components in industrial applications, known for their reliability and efficiency. These valves are key to managing fluid flow in complex systems, from chemical processing to water management and beyond. With technological advancements, they have become indispensable to ensuring systems operate at peak performance without compromising on safety or functionality.
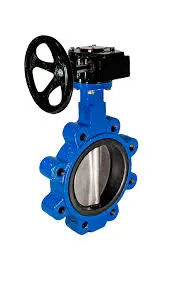
Valves have transformed drastically over the last few decades, evolving from basic shut-off mechanisms to sophisticated devices capable of withstanding high pressure and extreme temperatures.
High performance butterfly valves stand out in this evolution due to their unique design and optimized functionality.
In the world of high-performance industrial equipment, what truly sets these butterfly valves apart is their innovative design, which features a streamlined disc that allows for quick rotation with minimal pressure drop. This design minimizes resistance when the valve is open, which is crucial in systems that demand efficient flow with minimal energy consumption. The unique offset design of the disc also contributes to this, reducing the wear and tear on the valve seat, thus prolonging the valve's life and reducing maintenance costs.
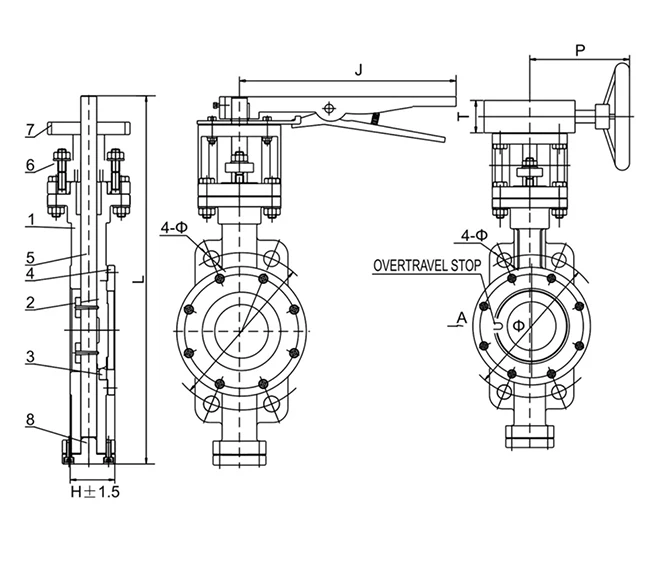
The materials used in high performance butterfly valves are critical to their functionality and longevity. These valves are often made from resilient metals such as stainless steel, carbon steel, or exotic alloys, which can endure highly corrosive environments often encountered in industries like oil and gas, chemical processing, and power generation. The anti-corrosive properties of these materials ensure that the valves can maintain their integrity over time, which is a critical factor for maintaining safe operations in various industrial applications.
In terms of expertise, manufacturers leverage cutting-edge technologies during the production process of these valves. Advanced computational fluid dynamics (CFD) tools allow for precise simulation of valve performance under various conditions, ensuring each valve can handle the stresses of its designated application. Additionally, rigorous testing procedures are applied, where each valve is subjected to extreme operational conditions to certify its durability and effectiveness.
high performance butterfly valve
Authoritativeness in this field is often demonstrated by industry standards and certifications. High performance butterfly valves typically adhere to global standards such as API 609, ISO 10631, and others, ensuring they meet the stringent requirements mandatory for industrial applications. Such certifications also enhance the credibility and trustworthiness of these valves, assuring customers of their quality and performance.
From an experiential standpoint, users have consistently reported improved system efficiency when integrating high performance butterfly valves into their operations. The ease of operation due to the valve's quick quarter-turn action and its ability to seamlessly regulate flow without significant manual adjustments have been highlighted as major advantages. Furthermore, due to their compact design, these valves require less space and can be installed in systems where larger valves might not be feasible.
Trust in these components stems from their proven track record in various industries. Case studies reveal how companies have drastically reduced maintenance costs and improved operational efficiency by replacing older valve systems with high performance butterfly valves. For instance, a petrochemical plant documented a notable increase in uptime and a reduction in operational interruptions post-installation, attributing these improvements to the valve's low maintenance and high reliability.
For businesses looking to optimize their fluid management systems, investing in high performance butterfly valves is a strategic decision. These valves are not just engineered for resilience and efficiency but are also a testament to modern engineering's capability to enhance industrial operations. As industries continue to evolve, so too will the technologies behind high performance butterfly valves, promising even greater efficiencies and innovations in the future.