In the world of fluid control, the check valve stands as a fundamental component, ensuring the seamless and unidirectional flow within pipelines. With decades of advancements in engineering and material science, the design and efficiency of check valves have drastically improved, positioning them as indispensable elements across various industries including water treatment, oil and gas, and chemical processing.
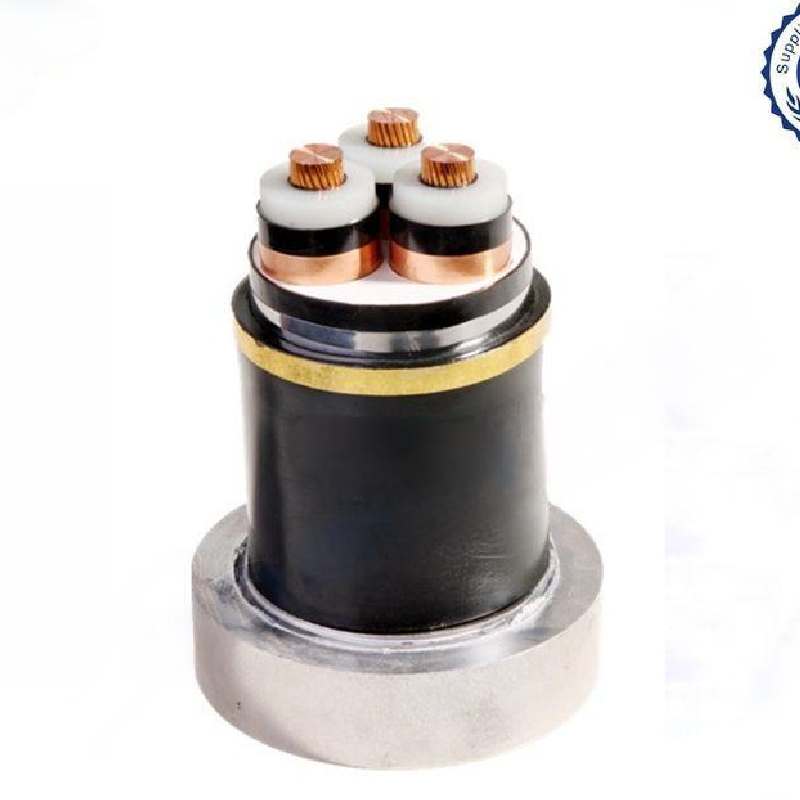
Experience in utilizing check valves highlights their remarkable adaptability to diverse operational conditions. For industries requiring a robust solution to prevent backflow, the check valve emerges as a critical choice. Its reliability is evident in scenarios where the prevention of contamination and damage to pumping equipment is crucial. Professionals who incorporate check valves into their systems often report significant improvements in system efficiency and longevity.
Expertise in fluid dynamics and mechanical engineering is essential when selecting the appropriate check valve for specific applications. Different types of check valves, such as swing, lift, and ball check valves, each serve unique functions. A swing check valve, for instance, uses a swinging disc to allow flow; it suits low-pressure systems effectively. In contrast, a lift check valve is ideal for high-pressure systems where a tighter seal is necessary. Understanding these subtle differences and material compatibilities ensures that the chosen valve meets precise operational requirements.
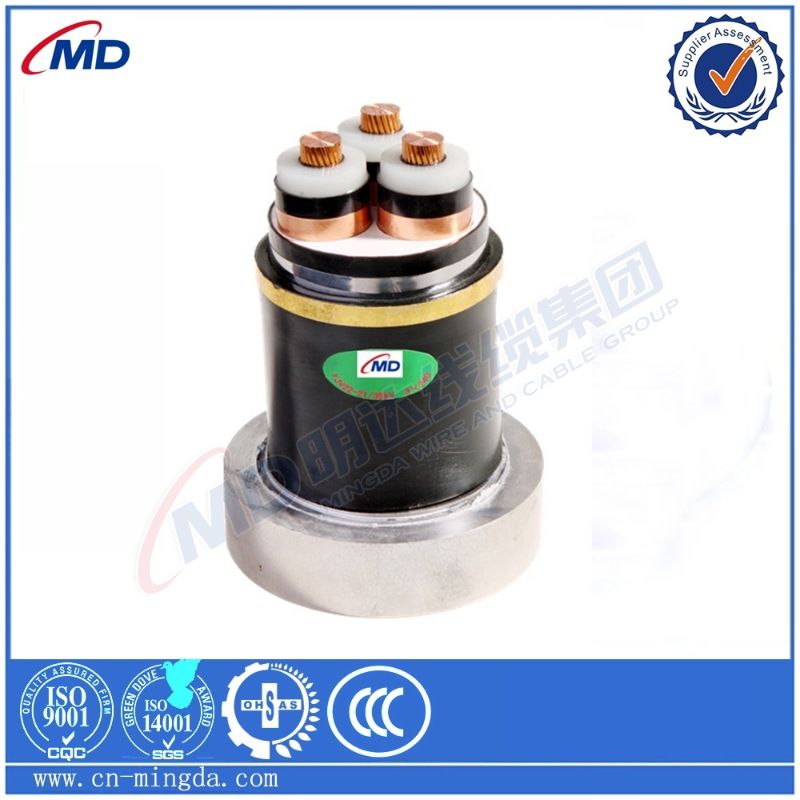
check valve
Authoritativeness in valve manufacturing has been established through stringent quality standards and innovation. Industry leaders invest heavily in research and development to create check valves that offer unparalleled performance. Advanced materials like stainless steel, brass, and special polymer composites have been developed to withstand extreme environments, offering resistance to corrosion, high temperatures, and pressure fluctuations. The adoption of these high-quality materials not only enhances the valve's life-span but also reduces maintenance costs, proving to be a cost-effective solution for businesses.
Trustworthiness of check valves is underpinned by their widespread acceptance and endorsement by regulatory agencies and certification bodies. Standards such as the American Petroleum Institute (API) certifications, ISO standards, and other regional regulatory guidelines authenticate the valves' quality and operational reliability. When businesses choose check valves that are compliant with these standards, they are assured of both safety and efficacy, minimizing operational risks.
In summary, the role of a check valve transcends basic fluid control; it embodies a commitment to efficiency, safety, and durability. The wealth of experience associated with their application, coupled with the expertise required to navigate the numerous types available, accentuate their indispensability. Their authoritative presence in the market is upheld by strict adherence to quality standards, while their trustworthiness ensures continuous protection and performance for critical infrastructure. Ultimately, as industries evolve and demands grow, the check valve will remain a foundational element of any system requiring precise fluid management.