Control valves have long been the unsung heroes in the world of industrial flow management. Beyond their basic function of regulating fluid flow, these components play a pivotal role in maintaining operational efficiency, ensuring safety, and optimizing the overall functionality of industrial systems.
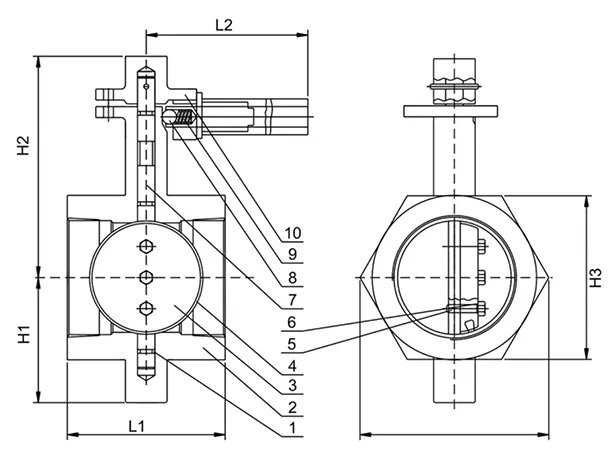
Experience speaks volumes when it comes to selecting and implementing the right control valve for specific processes. Over the years, seasoned engineers and technicians have found that understanding the unique characteristics of each fluid type is crucial. For instance, a valve that works exceptionally well in controlling gas flow might not be as effective for viscous liquids. This is where the intuitive grasp of experienced professionals comes into play, guiding decisions that can significantly enhance process reliability and reduce downtime.
When discussing expertise, the diversity of control valves cannot be overstated. The array consists of globe valves, butterfly valves, ball valves, and diaphragm valves, each with its own set of strengths and applicable scenarios. For example, globe valves are renowned for their excellent throttling capabilities, making them ideal for processes that require precise control of flow rate. Meanwhile, butterfly valves are often chosen for their compact size and efficient shut-off capabilities, which are perfect for applications with limited space and low-pressure drops. This depth of knowledge ensures that industry experts can recommend and implement the most suitable valve type based on the specific requirements of an application.
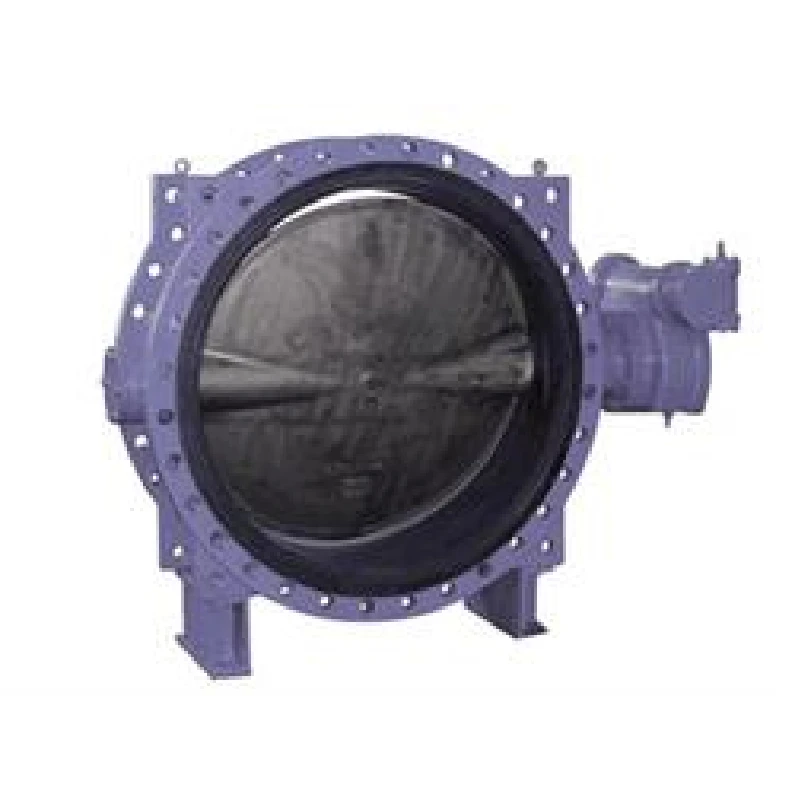
The authority behind the design and innovation of control valves is driven by rigorous research and development from leading manufacturers who continue to push boundaries in valve performance and resilience. These companies invest heavily in developing materials that can withstand corrosive substances and extreme temperatures, thereby extending the longevity and reliability of control systems. Industry standards and certifications like ISO 9001 also serve as a testament to a manufacturer’s commitment to quality and excellence, providing assurance to consumers and professionals alike.
control valve
Trustworthiness in the realm of control valves extends beyond product quality to encompass after-sales support and service. Reputable manufacturers and suppliers offer comprehensive support, ranging from professional installation services to routine maintenance and emergency repair solutions. This holistic approach ensures that systems not only run efficiently but also instills confidence among operators, knowing that expert assistance is readily available when required. Furthermore, the transparency in manufacturer-supplier communication strengthens trust, allowing for seamless updates and upgrades to valve systems as new innovations and technologies emerge.
In an age where energy efficiency and environmental responsibility are paramount, control valves have adapted to meet these challenges head-on. Modern designs incorporate smart technology, enabling remote monitoring and automated adjustments that optimize energy usage and reduce waste. This advancement not only contributes to a sustainable future but also offers financial benefits, as companies can significantly cut operational costs by reducing unnecessary energy consumption.
In conclusion, control valves are much more than simple flow regulators. They represent a convergence of experience, expertise, authority, and trustworthiness that collectively ensure efficient and safe industrial operations. As technology continues to evolve, so too will the capabilities of control valves, further cementing their role as integral components of modern industrial systems. Whether through enhancing energy efficiency or ensuring operational safety, the impact of control valves is profound and enduring, making them indispensable assets in the pursuit of industrial excellence.