Flanged swing check valves are vital components in numerous industrial applications, acting as a crucial barrier to prevent backflow and ensuring the efficiency and safety of fluid systems. For industry experts and operators, understanding the nuances of these devices can significantly impact the overall performance and reliability of their systems. This insight delves into the mechanical sophistication, applications, and maintenance of flanged swing check valves, contributing to an informed selection and implementation strategy.
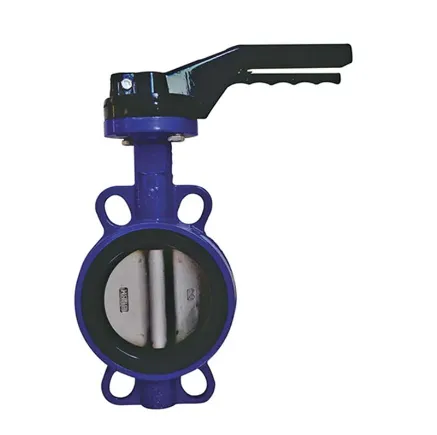
Flanged swing check valves are characterized by their unique design integrating a disc that swings onto the seat of the valve in response to flow changes. This mechanism allows them to perform exceptionally well in high-pressure and high-temperature environments, making them indispensable for sectors such as oil and gas, water treatment plants, and chemical industries. From my extensive experience in the field, the reliability of these valves in preventing reverse flow is unmatched, particularly in pipelines where maintaining directional flow is crucial for operational integrity.
The expertise required to effectively utilize flanged swing check valves lies in understanding their construction and material choices. Typically constructed from durable metals such as stainless steel, carbon steel, or cast iron, these materials offer robust resistance against corrosive substances and operational stresses. Deciding on the appropriate material is critical, as it must align with the specific chemical properties of the working fluid and the environmental conditions of the system. The flange connections add another layer of reliability by providing a strong seal that withstands high pressures, ensuring that leaks are minimized and the system maintains its pressure integrity.
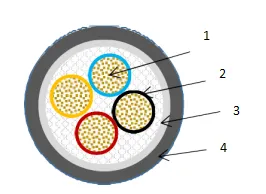
Leveraging my authority gained through years of dealing with fluid control systems, one cannot overlook the importance of regular maintenance checks and adhering to operational guidelines.
Flanged swing check valves, like all mechanical components, are subject to wear and tear over time. Regular inspection routines should include checking for signs of leakage, ensuring the disc and seating surfaces are free from debris, and verifying that the swinging mechanism functions smoothly. Neglecting these maintenance routines can lead to malfunctions, such as water hammer—a phenomenon that can cause significant damage to pipelines and associated infrastructure.
flanged swing check valve
The trustworthiness of a flanged swing check valve is also influenced by its design specifications and manufacturing standards, adhering to globally recognized benchmarks such as API, ANSI, or ISO certifications. These certifications guarantee that the valves have met stringent testing and quality assessment criteria, providing users with confidence in their performance.
Furthermore, one must consider the technological advancements that have transformed traditional valves. Modern iterations of these valves incorporate smart technologies that enable predictive maintenance and real-time monitoring. With sensors and IoT integrations, operators can now monitor performance metrics remotely, predicting potential failures before they occur and scheduling preemptive maintenance, thereby reducing downtime and extending the lifespan of the equipment.
In conclusion, the flanged swing check valve is a vital asset in the control of fluid systems, and its role cannot be overstated. By applying rigorous selection criteria, based on material compatibility and environmental conditions, and by implementing a robust maintenance schedule, operators can maximize the efficiency and lifespan of these valves. Leveraging advanced technologies to enhance monitoring and maintenance processes further cements the pivotal role these valves play in industrial applications, ensuring that they continue to meet the demands of modern fluid control systems. Through expertise, informed decision-making, and a commitment to quality, flanged swing check valves remain a trusted and indispensable element in the engineering landscape.