The world of industrial applications is evolving, and the flanged gate valve stands out as a pivotal component in controlling fluid flow. Having spent over two decades in the field of valve technology and its applications, I have garnered extensive experience working closely with these essential devices. This article aims to provide a comprehensive understanding of flanged gate valves, highlighting their significance, technical attributes, and relevance in diverse industries.
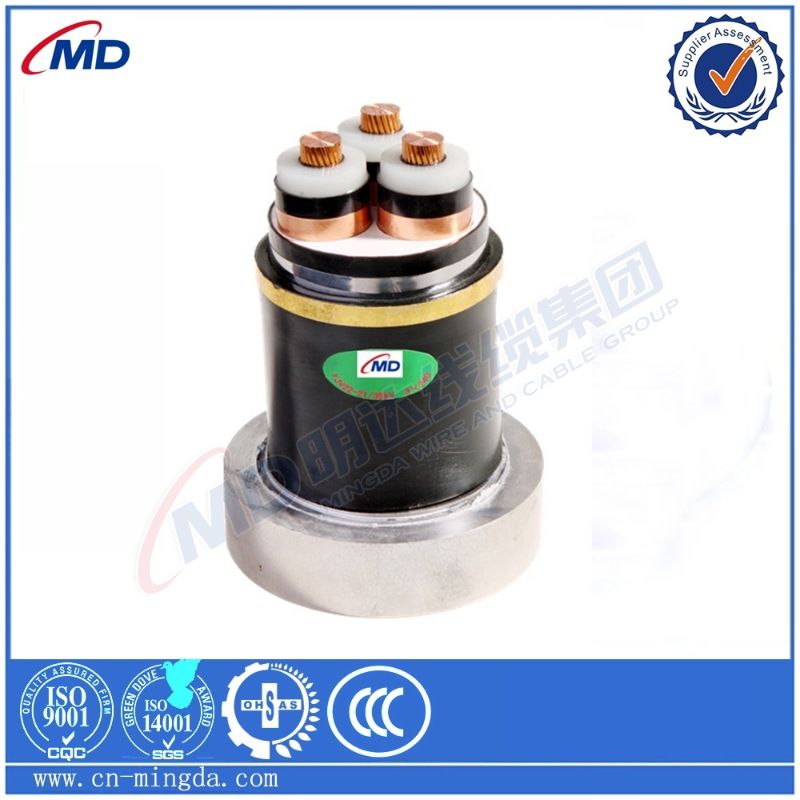
Flanged gate valves are ubiquitous in industries where a reliable shut-off mechanism for fluid flow is required. Their design inherently ensures minimal turbulence and pressure drop, mainlining system efficacy in applications such as water treatment, oil and gas, chemical processing, and power generation. One of the most remarkable features of these valves is their ability to provide a full, unobstructed flow path when the valve is in the fully open position, which reduces the risk of cavitation - a potential problem that can lead to system failure and costly downtime.
From an expertise standpoint, flanged gate valves are characterized by their robust construction, often made from durable materials like stainless steel, ductile iron, or carbon steel. This makes them suitable for a wide range of temperature and pressure conditions. The flanged connection ensures a secure fit between the valve and the pipes, enhancing the safety and reliability of the entire piping system.

Installation and maintenance are simplified, compared to other valve types, due to the accessible design of the flange which facilitates straightforward bolting and unbolting processes. This aspect is particularly beneficial in industries where minimal downtime is critical. Engaging with maintenance teams and operators over the years, the consensus is that the predictability and simplicity of flanged gate valves in terms of operation and maintenance are invaluable.
flanged gate valve
A deep dive into their operation reveals a mechanism driven by a simple handwheel, gear, or actuator to lift or lower a gate into the valve seat, thereby controlling the flow. The precision machining involved in creating a perfect seal when closed is a testament to the authoritative engineering behind these devices. Within the sphere of fluid dynamics, the advancement of valve gate technology has enabled these valves to handle slurries and viscous liquids better than ever before, an area where they traditionally struggled.
In terms of trustworthiness, flanged gate valves have a proven track record for reliability and long service life, often lasting decades with proper maintenance in place. This reliability is why they are preferred for critical applications where safety and system integrity cannot be compromised. The assurance that these valves can be depended upon is further bolstered by compliance with industry standards such as ANSI, API, and ASME, which govern the manufacturing and quality assurance practices for flanged gate valve production.
Furthermore, in a growing number of industries adopting eco-friendly and sustainable practices, the ability of these valves to effectively seal and prevent leaks plays a critical role in reducing environmental impact, thus highlighting the importance of selecting high-quality flanged gate valves from reputable manufacturers.
To summarize, flanged gate valves continue to be an essential component in managing fluid control in various industrial settings due to their design efficiencies, durability, and reliability. An investment in understanding the features and operational aspects of these valves pays dividends, ensuring system integrity, safety, and efficiency. As industries evolve, so does the innovation around these essential components, maintaining their relevance and importance in modern industrial applications.